The Abu Dhabi National Oil Company (ADNOC) new headquarters building, located in Abu Dhabi (UAE), recently completed, occupies a special place in the heart of the natural stone industry people for holding a unique record - it can probably claim to be the highest building in the world with an exterior façade of granite. The building has height of 342 metres and has 65 floors of offices. The building was designed by the US based largest architectural and engineering firm HOK, USA. The architects chose a wide range of natural stones in this project, in which engineering focus was on energy efficiency and the latest sustainable technologies, such as double skin facades and photovoltaic glazing.
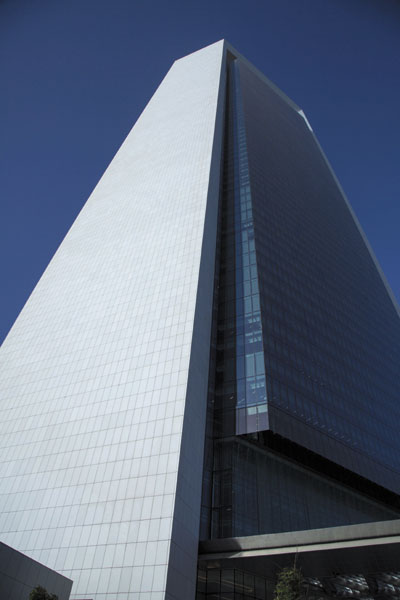
The two vertical sides of the portal arch serve as structural core that contains the fire exit stairs, goods lifts, and plant rooms and associated shafts. Their orientation to the East and the West provides shade from lower angle sunlight during the morning and late afternoon. The tower is now like a monolithic colossal sculpture that faces and contrasts with the crystalline blue water of the Arabian Sea.
Bethel White, from Rock of Ages quarry in Vermont, USA, was the granite chosen for the façade to give a ‘white tower’ look. 44000 sqm of the granite, in 40 mm thickness for façade wall cladding in flamed and water-jet brushed finish, and the large size of the stone panels 215 x 110 cm, was a special challenge, and was supplied by Nikolaus Bagnara S.P.A. Italy and Universal Marble and Granite Group Ltd, China and the final cut to size fabrication and delivery to site by AMG (Ascon Marble & Granite) Dubai. Installed by HAZ MARBLE AbuDhabi.
An additional 17000 sqm of Bethel White was procured from the Rock of Ages quarry, supplied by Nikolaus Bagnara S.P.A. Italy and all stones fabricated and installed at site by AMG (Ascon Marble & Granite) Dubai.
The interior stone panels were designed in large sizes, 215 x 110 cm, of 2 cm thickness.
Several different stones from different countries were also used, including Black Absolute granite from Gem Granites, (India), Grey Badajoz from Ingemar (Spain) for toilet floorings, Nero Impala from Savema (Italy) - these in slip resistant surface finishing, flamed and mechanically brushed.
About 3500 sqm of coloured marbles and onyxes were used at niches and greeting walls- Iranian Blue Onyx from Fujian BMG (China), Lapis Lazuli from Akrit Jewelcraft (India). Other materials used were Nero Impala, Blue Eyes and Marina Pearl from Savema (Italy), Forest Green and Forest Brown from Global Stones (India), Giallo Siena from Tognetti Gianfranco (Italy), Rosso Damascato from Treemme (Italy). Composite quartz from Cosentino (Spain) and Crystal Glass from Zenith & Co. (Singapore) were also used.
The company Vanello S.P.A., based in Carrara (Italy) processed the blocks into slabs and did the surface treatment in its factory. The final processing was done in the AMG factory in Dubai. During a period of 2 years a significant part of the AMG factory was fully dedicated to this project. AMG built up in its Dubai factory a dedicated dry lay area of about 500 square meters, equipped with removable cover roof for inspection and approval of the stone panels, in shady conditions and under direct sunlight as well, before the delivery to site. Hundreds of workers were employed for the execution of this project.
Under the supervision of the internal quality control management, many rows of stone panels were laid at once in order to avoid any possible deviance from the approved range. The quality control protocol contemplated the preliminary approval of AMG’s and BESIX Group’s QA/QC representatives and the definitive approval of Client’s and SMS’s Inspectors.
Further to their acceptance, the stone panels were delivered to site and taken over by the installer, the firm HAZ Marble LLC (Turkey). And here the second great challenge had to be won.
Contract documents specified a system that should perform accordingly with the severe parameters imposed by the design criteria and Abu Dhabi government’s construction codes. Architect, consultant and subcontractors actively participated in the development and building of the project's envelope with the principal entity of the design and construction team.
The high quality facade anchoring design and the further erection integrated through all phases the experience of the parts involved in the job. The anchorage method provides the innovative system of the tasks slotted on the back sides of the stone panels. This method worked well with the engineering requirements, facilitated the erection, increased the installation rate and finally guaranteed the safest result.
AMG developed its own anchoring system for the wall claddings. The anchorage method was based on special T-slots machines into the back sides of the stone panels, and the adoption of the T-31 bolts by the Coldspring Systems, USA. The laying of floors on a thin-bed system made of screed works on which stone was laid used adhesives supplied by Mapei, Italy.