Walter Denzel, info@dns-denzel.de
Unspecified residual moisture is the main reason for moisture-related flooring failures. A moisture profile, in combination with the equilibrium moisture content (EMC) which is reached under normal conditions of use, allows accurate measurement of the critical residual moisture content inside a building material. The best available technique of measuring critical residual moisture is the determination of the relative permittivity by HF (High-Frequency) methods. While each mixture of building materials aspires to a different equilibrium moisture content, it is necessary to determine its specific moisture profile. No correct and reproducible determination of the residual moisture is possible without knowing the thresholds of its equilibrium moisture content.
Initial situation
Man-made cement- or gypsum-bonded building materials consist of bonding agents, aggregates, sometimes additives, and water. Approximately 45% of the water volume used in preparation is bound within the crystal lattice of the material mixture (depending on temperature).Accordingly, 55% of the water volume is not required for strength or any other function of the component. However, this water volume must be transported via capillaries from the 5 cm or even thicker material layer to the material's surface where it can evaporate, provided that the barometric pressure is less than the water vapor pressure at the material surface (Brokamp, 2009).
So-called equilibrium moisture content (EMC) (in % of weight) for different material mixtures:
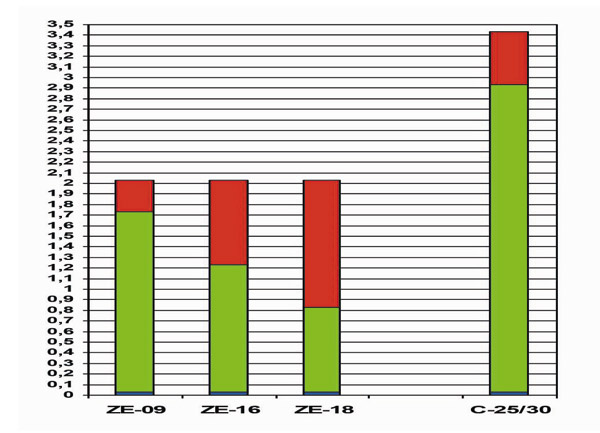
ZE-09 to ZE-18 are three cement screeds of different pressure resistance; C-25/30 is a concrete of strength class 25. The blue bar represents the "dry" material, the green bar the "safe" moisture equilibrium at 20 °C, the red bar the "hazardous" residual moisture. However, if a base coat or a coating of any other kind (e.g. screed) is applied before drying is complete, the drying process is interrupted or at least impaired. This causes an overpressure of the water vapour between material surface and underside of the coating. Depending on the temperature inside the material mass, this can cause damage to, or even destruction of the sealing layer (Denzel, W., 2007a).
Damage analysis
Evaporating water expands to 1.650 times of its volume when in liquid state. Even the smallest amount of water may constitute a moisture hazard, accordingly. The following formula may be used to calculate the hazard:
1 m2 of a 5-cm screed layer weighs approx. 115 kg (specific weight of 2,200 kg/m3). At a rate of 0.1% of water by weight, the screed contains approx. 115 g of water per square meter. (0.5% = 575 g; 1.0% = 1,150 g of water) At a temperature increase of 2 °C in the capillaries, these 115 g of water create an overpressure of 0.3 bar if the surface is sealed.
Methods of measuring moisture and problems occurring on site
The standard moisture profile of the individual material mixture allows any deviation on site (incorrect mixtures, compaction issues, layer thicknesses, local drying conditions) to be identified and evaluated for its relevance for potential damage. Also, the standard moisture profile helps to identify and allocate deviations of the formulation or of the raw material (Denzel, W., 2007c). Without knowing the material-specific moisture profile and the threshold for the balanced moisture at 20°C, it is neither possible to measure the current residual moisture nor to determine whether the material is "sufficiently dry" or "too moist" (Denzel, W., 2008a, Kuschel, M., 2012).
Capacitive moisture measurement using HF sensors (non-destructive); a high-frequency alternating field samples a volume of material located around two or three electrodes to determine the material - and especially the moisture-dependent capacity of the construction material. This method represents a special case of FDR (Frequency-Domain Reflectometry), where usually only one single frequency between approx. 100 kHz and 10 MHz is used. As a special form, the FDR method is applied in laboratory measurement devices where microwave resonators are used to determine the shift of resonance frequency and the change of bandwidth caused by the material to be used.
Destructive measurement methods have the following implications:
• They can only provide a snapshot (but sequenced measuring requires regular sampling, which is not feasible in practice).
• They cause delays (gravimetric evaluation).
• Delays are changing the original Material-Moisture-Content meantime.
• They cannot produce results that represent a total area of deviating moisture content.
DNS-Denzel moisture meter
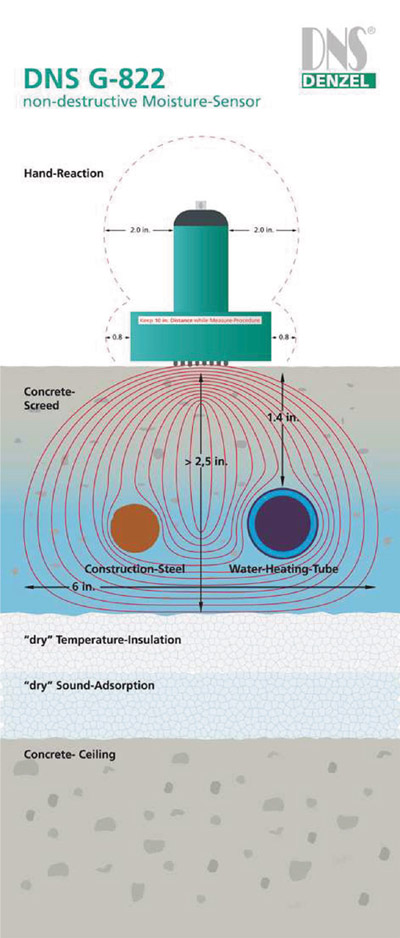
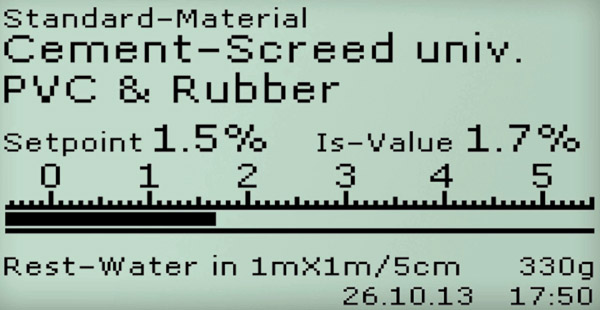
DNS-Denzel Feuchte-Messtechnik relies on the proven capacitive measurement method. Specifically designed sensor contacts provide optimal contact pressure on the sample material surface to ensure reproducible measurement results. Various device variants are available to cover the requirements of almost any application area. During measurement, an amplitude-stabilised signal with a sampling frequency of 3 MHz creates a high-frequency electric field to determine the capacity between the device sensors depending on the material's relative permittivity. On the basis of the material-specific calibration directly saved in the device memory, the moisture content relative to the dry mass is shown directly in % by weight. The calibration is based on comparison measurements of identical material formulations performed using the climate chamber method described. The effective measuring range of the devices allows them to be used for moisture measuring between 0 to 5% by mass of water within the building material. Temperature changes in the material within a range of approx. 10 to 40°C are not relevant. Thanks to the material-specific calibration (depending on the moisture profile) combined with the electronic stability of the moister-detector and the firm coupling of the sensors to the material surface, measuring accuracy is quite above average.
The reproducibility of the measured values exceeds 99%, provided that device calibration corresponds to the specific material. If the frame formulation of the material remains unchanged, the reproducibility of the measured values remains higher than 97%, even if raw material batches differ.
When used properly, this method currently represents the optimal test method of measuring moisture in a simple manner in the construction trade.
______________________________________________________________________________
Measuring Range: up to 10 % Moisture-Content.<
Measuring Time: 2 seconds.
Measuring Field Excitation over Spring-Contacts for uneven Surfaces.
Measuring Depth:>6 cm (> 2,5 inch) Concrete-Rebar and water-containing (heating) Tubes do not affect the measuring-results.
G-820-Box:125 X 83 X 35 mm (4,9 X 3,15 X 1,4 inch)
G-821-Senor:125 mm / Ø 81 mm (4,9 / 3,2 inch)
Weight: 710 g (in Box 1.710 g).
Display: Weight-% digital + analog.
Power Supply: 1,5-V-Akku / 3,6-V-Battery.
DNS-Denzel | Feuchte-Messtechnik | Am Wasserturm 5 | D-73104 Börtlingen
Sections