by Ángela Gonzalez Campos, Directora de Calidad, Prevención de Riesgos Laborales y Desarrollo Sostenible de Centro Tecnológico del Granito de Galicia
angela.gonzalez@ftcgranito.es
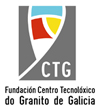
In the past materials were natural, coming from the environment, simple and adapted to the climatic conditions of the territory where the building was established. Because of the demands of society and the Industrial Revolution, the model of construction has changed, increasing the distance between the obtaining of raw materials and the location of its manufacture or construction.
It has been necessary to extract and process a great quantity of raw materials, to elaborate new materials and to treat a greater amount of construction and demolition waste, with the due energy cost. That is why, at present, the construction industry has made the use of materials with low environmental impact a priority.
The Carbon footprint is one of the environmental indicators most used to evaluate the environmental performance of a product or service and above all to establish comparatives between different products with the same functionalities.
This is the most appropriate indicator for measuring the potential global warming which generates the life cycle of a product, from the extraction of the raw materials to its use and the management of its waste.
The Carbon Footprint is defined as the amount of direct and indirect emissions of greenhouse gases (GHG) of a product or service throughout its life and is measured in equivalent emissions (kg) of CO2, the acronyms for this indicator is GWP (Global Warming Potential).
This quantification allows us to be aware of the impact that our activity and granite products generate on global warming, turning the carbon footprint into a tool of awareness of great value. Nowadays, it is already seen as a differentiating element for organizations that decide to commit to the environment and bet on the development of sustainable activity.
Some advantages which this environmental indicator presents against others are the following:
- It is an easy to understand indicator, the Carbon Footprint measures the equivalent CO2 emissions of a product so that the less Carbon footprint, the less global warming potential associated with that product.
- It can be applied to all kind of products, processes, companies or activities, thus it may be calculated in respect of the most complex process as well as the most simple and usual one.
- It allows for carrying out of benchmarking of products in a relatively simple way, giving us information about those that present a smaller impact on global warming and are therefore more efficient from the environmental point of view.
- The reduction of the Carbon footprint usually implies a reduction in energy use, an increase in efficiency, better management of resources, better waste management, etc., so it is a quite complete indicator regarding the eco-design of products and services.
· There are various calculation methods, all of them equally valid, that we can select according to our needs and adapt to our products. It is important to know the calculation methodology and its scope when comparing the carbon footprint of different products. It should be noted that the smaller the scope is and less processes or products are included in the study, the carbon footprint will have a lower result, but will give us incomplete and unrealistic data. In this comparative, the carbon footprint values refer to a scope of Cradle-Factory gate for all selected products.
Selection of environmental product declarations
To carry out the comparative of the Carbon footprint for the different construction products that were included in the study, current Environmental Declarations of Product (DAP) guaranteed by national and international Program Management Entities have been chosen, of type III (eco-labels).
The information contained in a DAP is based on the implementation of a global and multicriteria evaluation of the environmental impacts of a product from its origin to the end of its useful life. This is done using the Life Cycle Analysis method (ISO 14.040-ISO 14.044), following the rules that are set out for each Product Category on a scientific and regulated basis.
The parameters that are analysed are diverse although for this analysis we have selected the data in respect of the indicator of the Global Potential Warming (GWP) which will inform us about the Carbon Footprint of the different products.
The selected systems are highly regarded and have the highest number of Product Environmental Declarations for construction products:
· The Spanish GlobalEPD from AENOR
· The Spanish DAPc from Agenda de la Construcción Sostenible
· The German IBU from Bauen und Umwelt Institute
· The Swedish EPD International AB from the International EPD System
1. Interior flooring
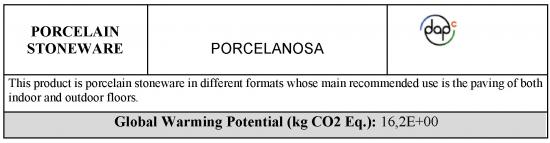
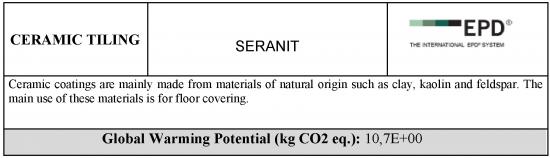
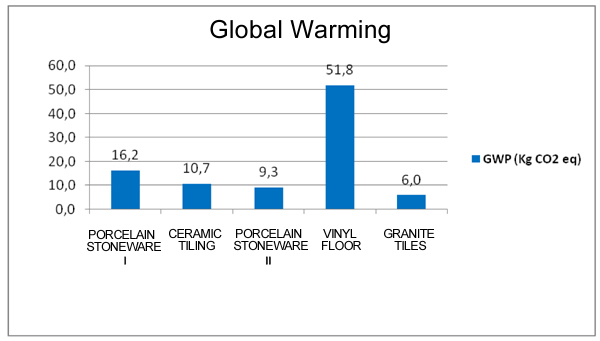
Vinyl floors present the greatest global warming impact of all pavements that have been compared. This is followed by ceramic materials and granite tile, which has the lowest value of this indicator in reference to the carbon footprint.
PVC, the main component of vinyl floors, is made from fossil fuels, non-renewable resources. In addition, the production of both chlorine and ethylene gas waste enormous quantities of energy implying a higher carbon footprint for these products. The ceramic industry uses high-calorific power fossil fuels such as natural gas that directly impact on global warming.
At present, most of the granite constructive products come from blocks that have been sawn with the Best Available Technology, such as the multiwire machine. It is assumed that the equipment gives an energy efficiency much superior to the looms of steel sheet that allow them to obtain low consumption of energy by square meter.
If the granite varieties are of national origin, relatively close to the industry, the carbon footprint continues to be reduced to the values that are shown due to the reduction in the impact on transportation.
Porcelanic Stoneware - Porcelanosa
Ceramic tile - Seranit
Porcelanic Stoneware - Ibero Alcorense
Vinylic floor - Kardean
Granite tile
2. Wall coverings
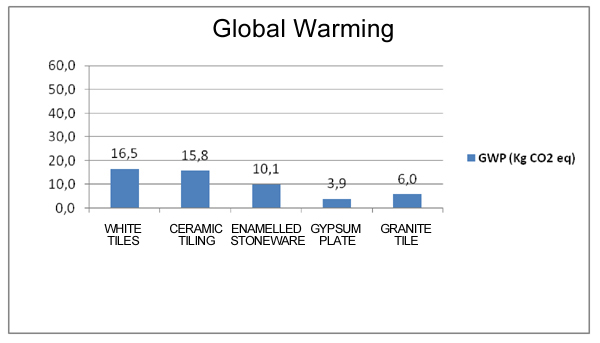
The three ceramic materials have similar values in respect of carbon footprint the highest being for the white tile coating. These materials are followed by the granite tile, processed in the same way as in the previous section and lastly, with the smallest impact in this category, we have the gypsum products.
The gypsum plate is not usually a coating product but a partition or space divider, but the product studied is designed to act as a coating on interior walls presenting different characteristics of density, colour ... etc. These materials are composed of gypsum in 94% of the total of its composition and do not present additives of risky or dangerous substances, besides its productive process is not intensive in energy consumption.
White tiles - Colorker
Enamelled Stoneware - Novogres
Ceramic tile - Seranit
Granite tile Gris Mondariz
Gypsum plate - Bristish Gypsum
3. Facades
The glass panels are presented as the building facade product with greater impact on global warming, double the value of the next one, which is the facade of steel panels. It follows, with less difference in value, the facade made with prefabricated concrete. These three products would be at the top as the most impactful in terms of emissions of greenhouse gases. With much lower values appearing, for the facade of glass resins, the facade of stoneware and finally the facade of granite - which shows the best carbon footprint and the least impact in this category.
Glass is made from sand, whose main component is silicon oxide, other substances such as potash, lime and other bases are also needed. Sodium gives it some ease of fusion and calcium provides it with chemical stability. Once the components are mixed, they must be melted. Temperatures that reach 2000ºC are needed, and then the glass sheet is formed on a tin bath, a process that takes place at approximately 1000ºC. This process is very intensive in energy consumption hence the high values of some impact categories.
The steel facade also has a high carbon footprint due to its steelmaking process where electric arc furnaces are used to melt the raw material with high energy consumption and CO 2emissions.
Porcelain Stoneware facade - Mythage
Precast concrete facade - Aggregate
Glass panel facade - Schott
Glass resins facade - Sto
Steel panels facade - Kingspan
Granite plate facade Silvestre
4. Ventilated facade
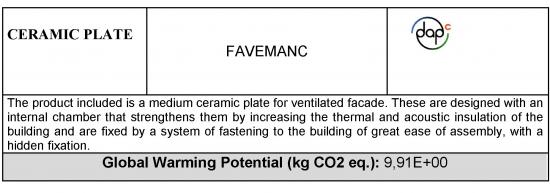
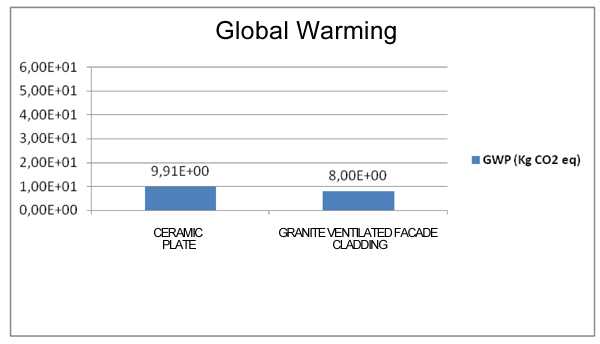
Pieces of granite for ventilated facades have slightly lower carbon footprint values than those for ceramic tiles.
As we have discussed in other sections, the introduction of multi-threaded machines in the granite sector has led to the reduction of energy consumption by half in the block sawing phase, the most energy intensive.
The good results obtained by all the granite construction products derive from the wide variety of granites that exist in Spain and in the north of Portugal which implies that the energy consumptions of transport from the quarry to the factory are reduced considerably against imported materials.
The baking of the ceramic products is one of the most important stages of the manufacturing process, since a great part of the characteristics of the ceramic product depend on it. This is a stage of high energy consumption since the kilns used can reach up to 1500ºC to achieve vitrification of porcelain and glazing.
Ceramic plate ventilated facade
Granite ventilated facade